Wood Frame vs Steel Frame Shop – Which Costs Less Overall?
When planning a new storage building, workshop, or other utilitarian structure for property needs, owners face a classic decision – wood framing or steel. Looking purely at upfront price points, basic dimensional lumber seems the economical choice. But factoring in lifespan maintenance realities and replacement costs down the road, steel emerges as the clear value winner in the long run.
Initial Material and Build Cost Comparison
For simple small-scale utility structures under 500 square feet, the material price difference lands reasonably close. Engineered wood trusses and stick framing ring up modestly cheaper than hot-rolled structural steel shapes and sheathing from American Barn. Though for anything larger or commercial grade, steel gains significant cost advantages needing less structural enhancement.
Regarding construction, basic wood builds frame up faster to lock in walls and roofing sooner. This appeals to DIYers tackling things solo over weekends and evenings. But crews putting up prefabbed rigid steel frames take similar site durations overall. The modular bolt-together aspects also reduce skill demands once erected.
Maintenance Realities Over the Years
Here is where wood fails miserably over time, requiring frequent upkeep and continual repairs that steel structures simply don’t need thanks to innate material ruggedness. Significantly slower deterioration makes steel frame shops virtually maintenance-free for over 50 years while wood buildings beg constant upkeep after just 10-15 years.
Additionally, steel stands up to punishing shop environments and abuse much better by resisting moisture, UV damage, pests, and force impacts without issue. It also never rots, warps or attracts mold – the bane of all wooden structures exposed to weather and use. This discrepancy translates into tremendous cost advantages as decades pass.
Some of the top benefits of building a shop or garage with pre-fabricated light gauge steel are:
1. Modular & Fast Builds – Light gauge steel framework is customizable and bolt-together simple for rapid build time. Minimal skill/equipment needed compared to stick framing.
2. Uniform Building Materials – All lighter-gauge cold-formed steel components coordinate for consistent strength and loading capacities across the structural skin.
3. Thermal Efficiency – Steel envelopes insulate space better than wood structures with thermal breaks and less air infiltration between durable panels.
4. Mold & Pest Resistance – Steel does not rot, warp, attract termites or enable mold growth from humidity like wood framing. Exceptional resistance for garages and shops with high moisture.
5. Flexible Designs – Steel kits can be custom designed and engineered to fit your specific needs, Precision steel standard profiles accept vertical/horizontal extensions and expansions easily with matched engineering integrity using the same gauges and load ratings. the options and flexibility in designs are unparalleled.
6. Project Cost Savings – Light gauge steel is easily DIY friendly saving homebuilders 50%+ over hiring framers. Material budgets gain discount flexibility with volume purchasing, inventorying, and simplified logistics.
7. Longer Lifespans – Steel buildings stand strong over 75 years negating the maintenance and replacement demands of wood frames lasting only ~25 years. Decades of use amortizes the initial investment favorably.
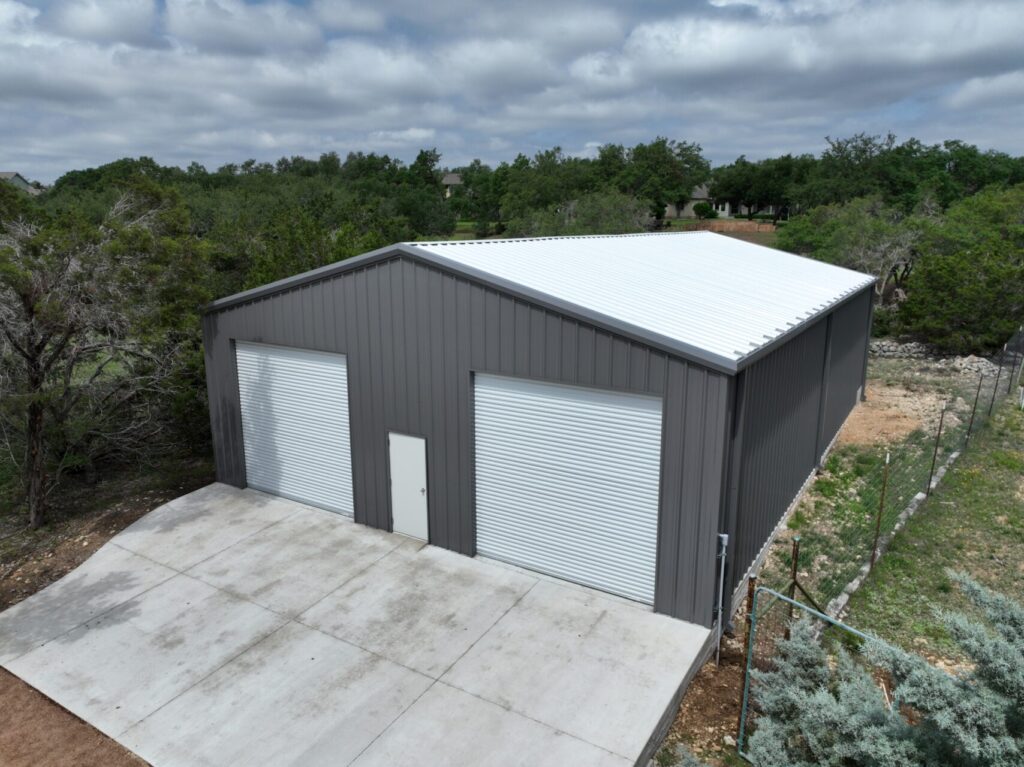
wood enjoys a smaller initial price tag but steel buildings deliver far lower total cost long haul. Their near maintenance-free durability provides reliable infrastructure, especially on structures built to handle demands. So do the math realistically when evaluating the total cost of ownership. Over likely decades of use, steel invariably wins out.